The creation of an ERDEN rug is the marriage of artistry and technology. To ensure the highest quality and consistency, ERDEN utilizes a data-driven system to manage and track the production process shared between ERDEN’s Chicago and Nepal offices in real-time. Working in a queue, every step is documented to ensure exact coordination throughout the production process at all times.
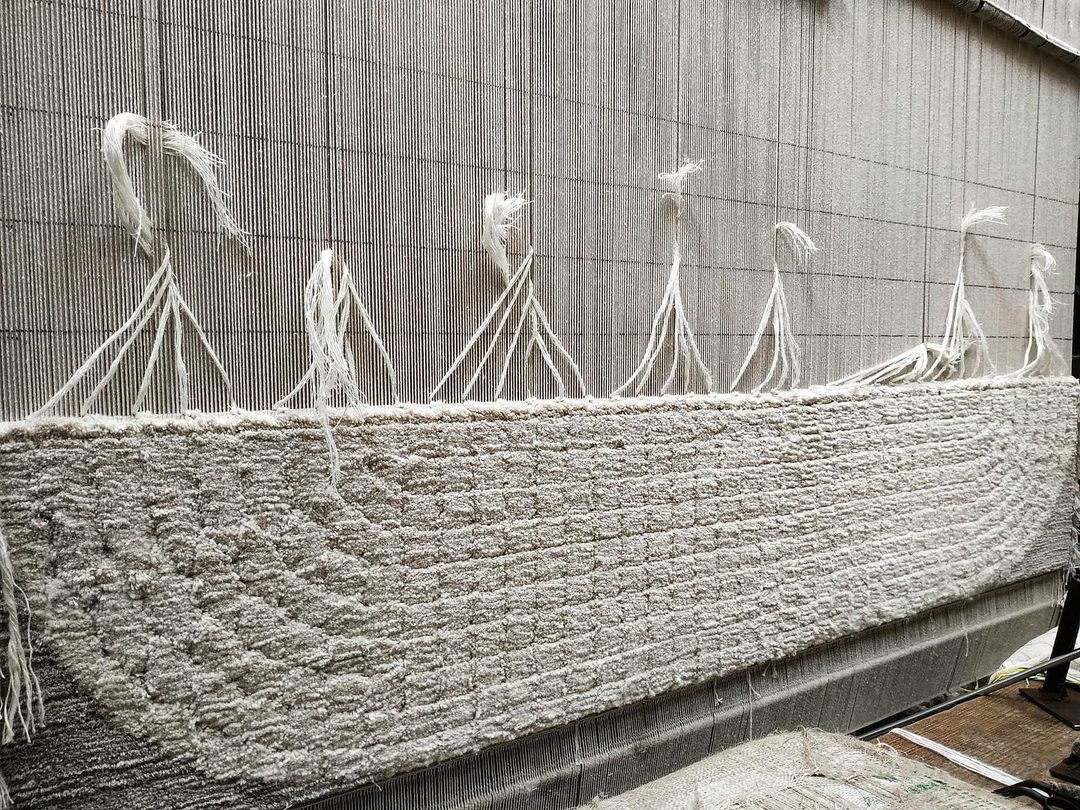
Rugmaking
Fibers are disentangled, cleaned, and prepped for spinning.
Cleaned and combed fibers are handspun into soft, lofty yarn of varying fiber lengths. Yarn can be spun very fine, or very thick depending on need.
Yarn is submerged in vats of dye by color match experts. The process of dyeing can take anywhere from one to two weeks.
Woven as a Tibetan weave or Flatweave. A Tibetan weave is hand knotted and woven from knots in sequential rows onto a warp under tension. Flatweaves are thinly hand woven on horizontal looms. If the design incorporates metal inlays, negative space is left during the weaving process, to be embedded upon arrival in Chicago.
Looms are checked bi-weekly, for the entire duration of the rug’s production. Photos and notes are taken to carefully document progress, which is available to designers and showrooms.
Every rug or strike off has two corresponding control samples produced, one being sent to the Chicago office and the other kept at the Nepal compound, ensuring accurate archival reference for subsequent needs.
Looms are checked bi-weekly, for the entire duration of the rug’s production. Photos and notes are taken to carefully document progress, which is available to designers and showrooms.
Every rug or strike off has two corresponding control samples produced, one being sent to the Chicago office and the other kept at the Nepal compound, ensuring accurate archival reference for subsequent needs.
Washing removes excess pile, yarn and reduces shedding. Stretching helps shape the rug and ensure the sizing is to specifications.
Any final corrections are made at this point. Pile is trimmed, edges are wrapped, and colors are corrected, if needed.
One of ERDEN’s pillars is quality and throughout the production process, numerous steps are taken to ensure consistent quality. Once production has completed, a rigorous final inspection process is conducted in Nepal and again upon arrival in Chicago. Two team members at each office ensure all designs are matched to ERDEN’s standards and specifications.
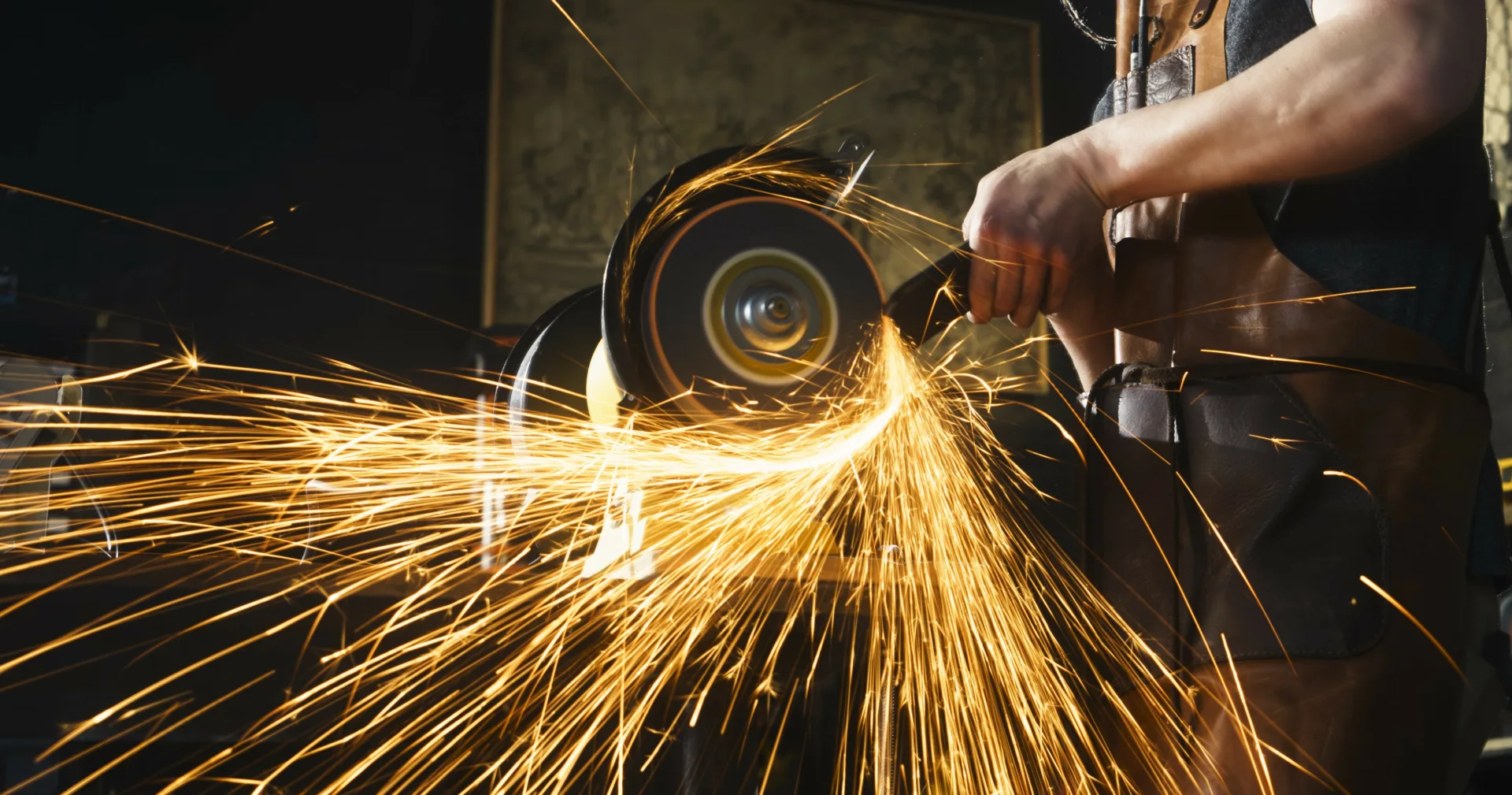
Metal
The merging of metal and fiber is strategically designed as a study of an antonym of materials, using the fiber as a barrier for comfort and the metal as an anchoring design detail. ERDEN continues to experiment with new processes in technically exciting and intellectually informed ways. All metal inlays are fabricated and embedded by craftsmen in Chicago.